July 26, 2022
Imagine: It’s your first day as a service technician. You’re standing in front of a broken machine in urgent need of repair. Your only tool is a cumbersome, outdated paper manual that’s clearly passed through the hands of dozens of employees before you. You thumb through the pages only to find the instructions you need are missing, evidently torn out. What do you do?
It's an all too familiar scenario for organizations dealing with the growing industrial skills gap. The problem is especially acute in Manufacturing due to an aging expert workforce, rising complexity, outdated training methods, and continued reliance on decades-old machines in many of today’s factories. As competition and globalization intensify, the million-dollar question is: How do manufacturers recruit, train, and empower the next generation of skilled workers when the skills they need are rapidly changing?
Best-in-class manufacturers have turned to Augmented Reality (AR) to develop and future-proof the skilled workforce. In the following use cases, real companies use AR to facilitate skills development while alleviating the impact of the industrial skills gap on their operations today.
BAE SYSTEMS
Sector: Aerospace and Defense
Application: WORK INSTRUCTIONS + ONBOARDING
British multinational defense, aerospace, and security company BAE Systems produces the HybriDrive hybrid electric propulsion system. As demand for reduced emissions grows, transit agencies are putting more HybriDrive-powered buses on roads across the globe. To increase production, BAE would need to teach new hires to assemble complex bus batteries quickly and error-free.
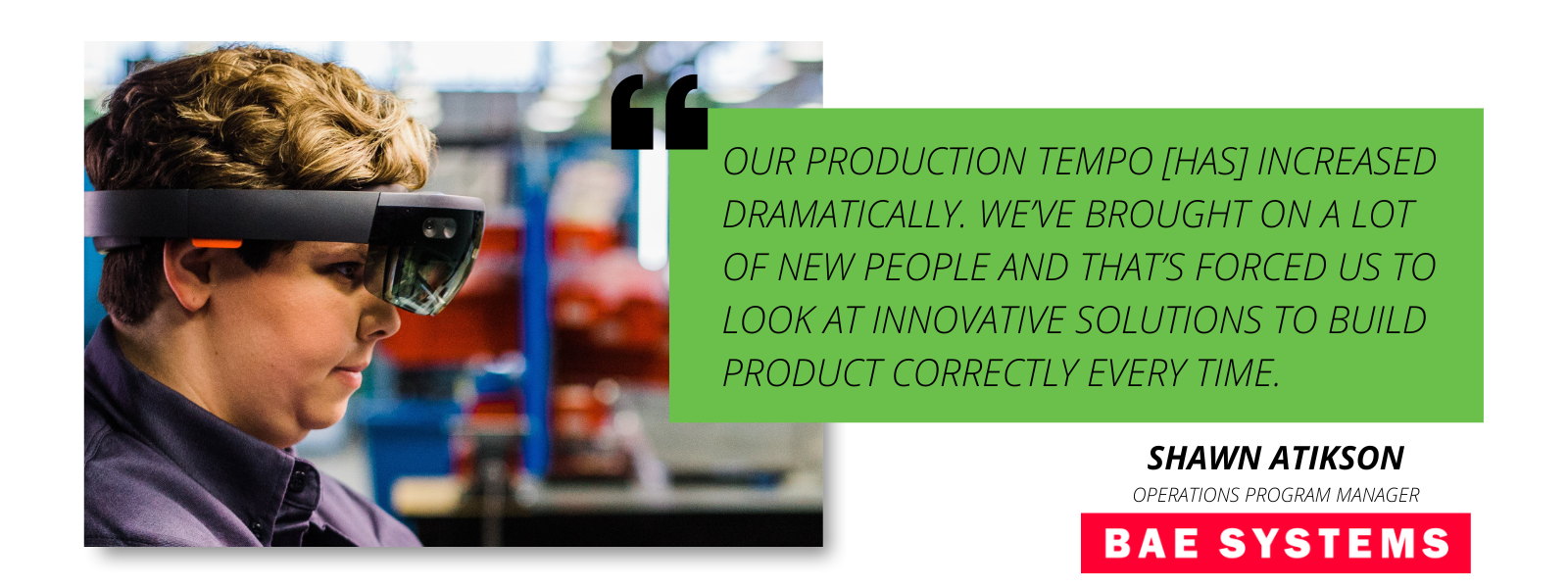
BAE Systems uses Vuforia Studio, a flexible and efficient solution for turning existing 3D models into augmented reality work instructions. BAE’s subject matter experts cost-effectively create immersive 3D work instructions in hours, not weeks, for delivery via Microsoft HoloLens. Displayed in context on the plant floor – heads-up and hands-free – these 3D digital instructions take workers through each step of the battery assembly process while effectively training them on best practices and reducing errors.
By anchoring digital information to the real production environment in front of the user, augmented reality eliminates the conceptual gap associated with following instructions on a 2D page or screen. Moreover, by replacing paper documents, AR allows BAE Systems to “walk the walk” of its customers working towards zero emissions.
Results: Battery assembly time cut in half; 30-40% more efficient training at a tenth of the cost of traditional methods.
BID GROUP
Sector: Forestry Equipment
Application: REMOTE ASSISTANCE
North American BID Group is a leading supplier of wood processing machinery with a global customer base. Prior to 2020, the OEM’s service experts traveled to customer facilities to carry out maintenance in person, relying on phone, email, and text message to communicate with one another. Then COVID-19 hit.
While describing problems over the phone may suffice for experts, phone calls and photos are inadequate to explain the inner workings of an industrial sawmill to an inexperienced technician. With its experts unable to travel, BID needed a way to empower customers and local field techs to service their own equipment with remote assistance from the company’s SMEs.
BID Group equipped its customers with RealWear augmented reality headsets preloaded with the Vuforia Chalk application. The combination makes it possible for customer staff to visually troubleshoot problems with BID experts from anywhere in real time. Live audio and video permit the expert to see what the end customer or local technician is seeing through the RealWear headset, guide him or her to a resolution, and even digitally annotate the screen to point out specific parts. With hands-free, on-demand access to remote expertise, even a technician with minimal experience can repair advanced machines.
Vuforia Chalk is now part of BID Group’s aftermarket services. What’s more, AR enables BID’s expert workforce to service a higher volume of customers than previously possible, effectively scaling their expertise globally.
Results: Faster issue resolution, reduced customer downtime, increased workforce productivity, and reduced travel costs.
.png)
HARPAK-ULMA PACKAGING
Sector: Packaging Machinery
Application: PREDICTIVE MAINTENANCE + TRAINING
Harpak-ULMA provides packaging technologies to a wide range of customers in the food, medical, personal care, and industrial industries. For many of them, chronic talent shortages and high turnover are raising the stakes of new hire training and machine efficiency, prompting Harpak-ULMA to leverage PTC's Vuforia Enterprise AR software suite to improve service quality.
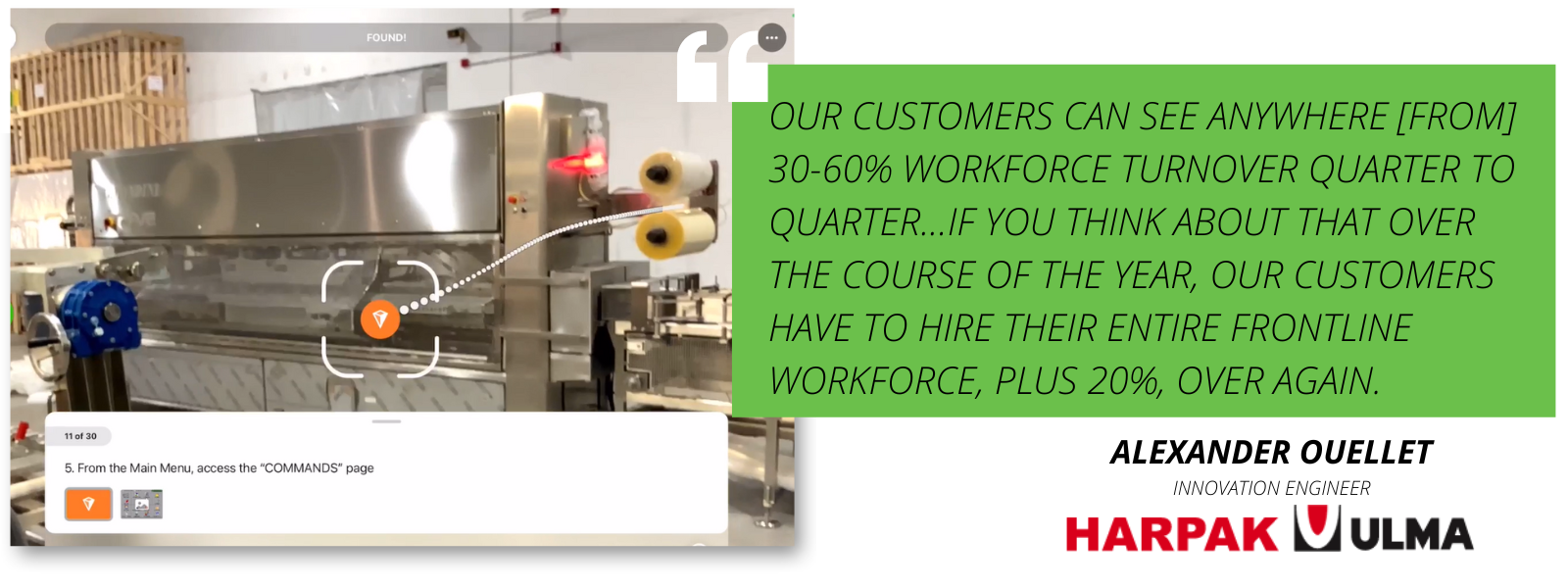
Harpak-ULMA uses Vuforia Chalk (see above), Expert Capture, and Instruct to create visually-based training and work instruction solutions that build desired technical expertise while driving overall packaging equipment performance.
The combo of Vuforia Studio and Internet of Things (IoT) data from enterprise systems provides real-time machine visibility, traceability, and context. At the onset of equipment failure, for instance, Vuforia can guide the operator to the problem, trigger the right augmented repair sequence, and verify the work is done correctly. This helps Harpak’s customers avoid unnecessary downtime (saving tens of thousands of dollars per minute) and effectively manage and upskill their scaled-down workforces.
Results: Increased new hire proficiency, faster time to repair, higher output, error reduction, revenue growth, and better labor retention for customers. Business differentiator for Harpak-ULMA.
HENKEL
Sector: Consumer Goods and Industrial Adhesives
Application: REMOTE ASSISTANCE + KNOWLEDGE TRANSFER
If you don’t know Henkel, you surely know brands like Dial and Persil in the Laundry & Home Care unit of its business. Before 2020, this unit relied on frequent expert travel to support production and service teams across the globe. As COVID accelerated, Henkel sought a speedy solution to maintain the same level of global support and uphold its culture of active knowledge transfer.
Henkel chose Vuforia Chalk, an out-of-the-box AR remote assistance app compatible with the devices Henkel employees already used. No need for new equipment or stringent security testing meant that Henkel could quickly roll out Chalk to more than 30 plants in just six months.
It takes only minutes for a frontline worker to download Chalk and begin sharing his or her view with a remote expert. In addition to verbal guidance, the expert can digitally annotate the user’s screen to clarify directions. Later, a recording of the video support call can be referenced in the field or used as training material. In this way, Henkel has managed to step up efforts to transfer years’ worth of expert knowledge to the next generation as its most experienced staff near retirement.
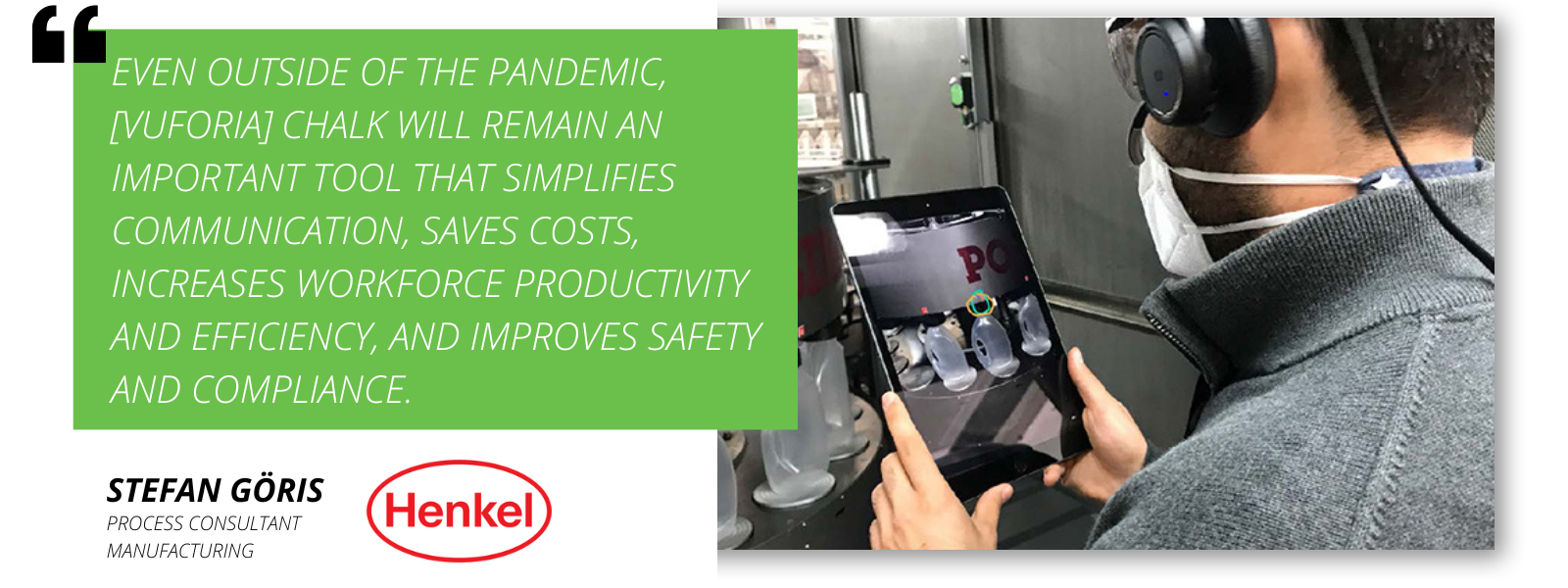
Today, around 200 Henkel employees use Chalk for both internal and external support. RealWear headsets are the next logical step, as AR spreads further into the company’s business.
Results: Rapid time to value; improved communication, reduced operational costs, increased productivity and efficiency, and improved safety and compliance.
INTERTAPE POLYMER GROUP (IPG)
Sector: Protective Packaging and Industrial Tapes
Application: KNOWLEDGE CAPTURE + TRAINING
If you’re a frequent online shopper, then you’ve probably interacted with IPG’s products before. After connecting its biggest pain points – quality defects, safety issues, onboarding, and downtime – to insufficient training and retiring experts, global packaging company IPG looked for a way to capture and scale the knowledge of its remaining expert workforce to both new and existing employees.

Rather than film basic training videos, IPG had seasoned operators use Vuforia Expert Capture to record changeovers, inspections, and other processes to turn into standard visual work instructions. On the plant floor, new workers view the augmented instructions via mobile device or RealWear headset, learning to perform tasks while also validating and documenting their work. Thus, Expert Capture enables IPG to provide more memorable and consumable on-the-job training content for a younger workforce.
What began as an effort to preserve domain knowledge and onboard new employees has helped IPG foster a company culture of training and development (upskilling) that’s attractive to younger generations who value opportunities for career advancement. IPG even uses HoloLens as a recruitment tool to show job fairgoers what it’s like to work with AR in the plant.
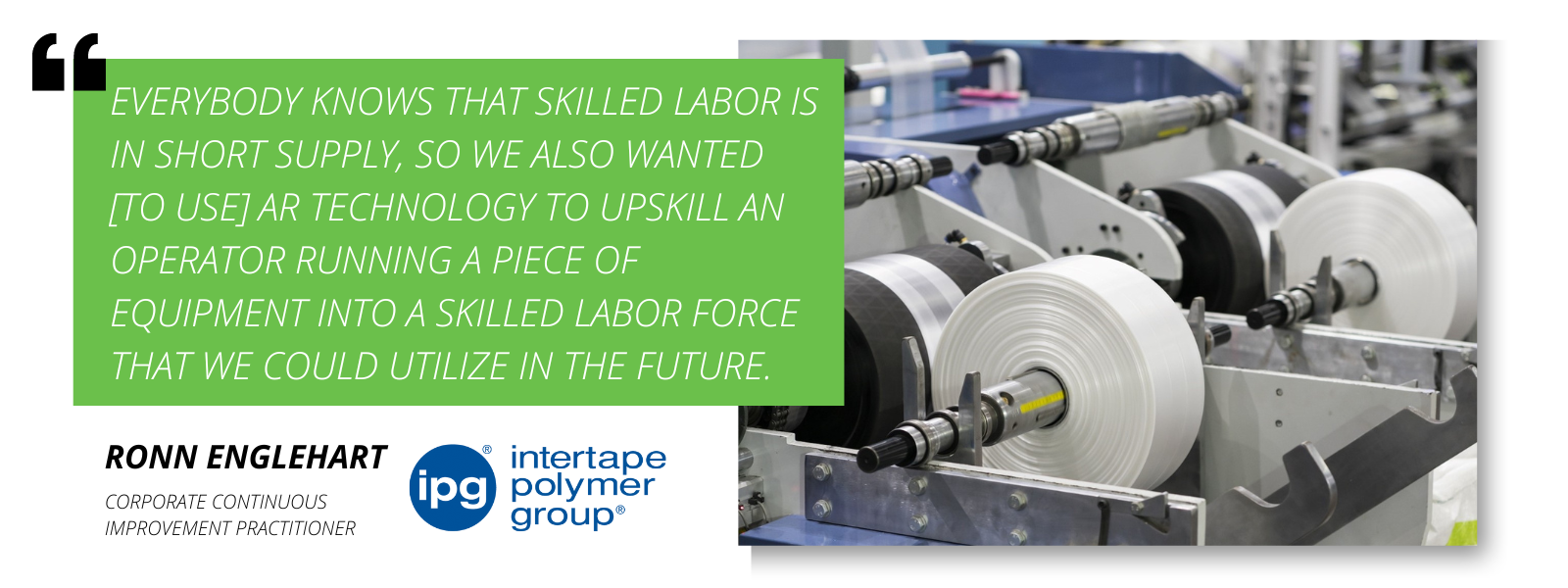
Results: Reductions in idle time, scrap, changeover time, and turnover; faster time to proficiency; improved safety, compliance, and talent acquisition.
VOLVO GROUP
Sector: Automotive
Application: WORK INSTRUCTIONS + DIGITAL THREAD (IIoT)
Swedish multinational company Volvo Group prides itself on the quality of the trucks and industrial engines it produces. Until recently, engine quality assurance (QA) was left in the hands of only the most experienced technicians. Increasing product complexity and customization, however, led Volvo to rethink QA training and the QA process itself.
Training new operators on complex inspection procedures used to be a five-week, paper-based process. You can imagine the cognitive load for trainees and the time and expense of updating and printing new materials. Volvo adopted Vuforia Studio to transform QA training into an augmented reality experience for the HoloLens 2. In addition, the company uses PTC’s ThingWorx platform to create a digital thread that essentially keeps track of custom configurations (real-time data synchronicity) and gains actionable insights.
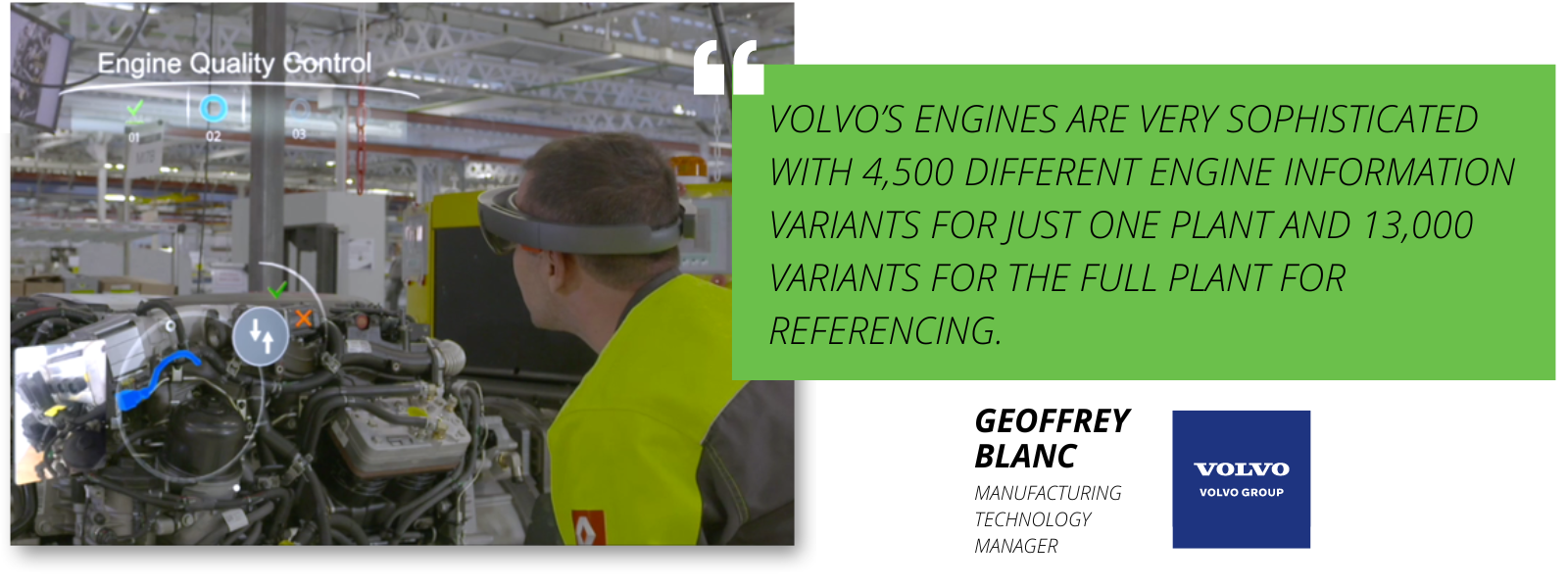
With Vuforia AR and ThingWorx, QA workers now always have access to the most up-to-date engine configurations in 3D directly on the physical engine. The solution also creates a real-time feedback loop: QA techs capture defects with HoloLens, which is sent upstream to improve future engine designs and manufacturing. Above all, Volvo has achieved greater flexibility and agility in response to shifting market and customer demands.
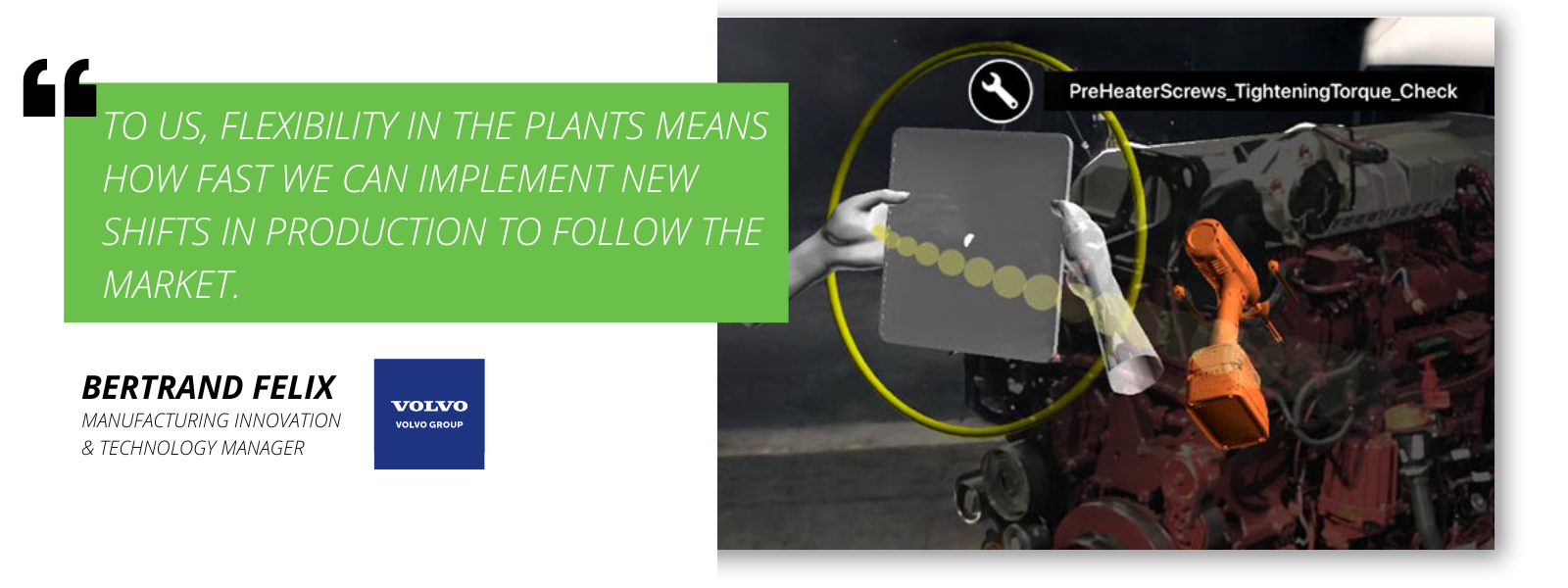
Results: QA training time reduced from 5 weeks to less than 2; checklists updated for new engine variants in 1 hour (used to take over a day); thousands of Euros in savings per quality station annually; improved recruitment; closer to Volvo’s 0 Part Per Million (PPM) quality goal.
Conclusion
Ultimately, the industrial skills gap is a workforce challenge. To fully overcome it will require significant improvements in recruitment, onboarding, training, information access, communication, knowledge capture, documentation, upskilling, and retention—all areas in which manufacturers are seeing clear returns from Augmented Reality.
What’s clear from the use cases above is that augmenting workers is inextricably linked to an organization’s agility and profit. Get started with augmented reality today…
