May 20, 2020
I recently had the opportunity to interview Kelly Ireland, Founder & CEO of CBT. CBT is bridging the gap between operational technologies and information technologies with groundbreaking projects like the Refinery of the Future at Texmark Chemicals. Check out CBT at EWTS Everywhere this October and read on to learn more about the company’s inspiring woman founder:
Q: To begin, could you provide a little background on yourself and your career?
A: Sure, I was a STEM girl way back before STEM was even a thing. I was a heavy math and science person in high school, went into college and just, you know, wasn’t loving it. I had the opportunity to become a coder/developer; the company I was working for part-time sent me to IBM school and I became an RPG II and III programmer for their minicomputer. After that, I just kind of stayed in tech and transitioned through a multitude of different occupations and companies and eventually ended up in sales. I went through a few different companies because in the 1990s most of the tech companies in IT or VARs (valued added resellers) were buying one another and another and another. So, I ended up with multiple owners and then got to the point where I felt that I knew a better way and opened CBT.
Q: Well, that gets to my next question: When did you start CBT and why? What was CBT at the beginning?
A: I opened CBT in 2001, mid-year. There were a lot of acquisitions at the time, a lot of uncertainty. I had a unique client and it was right in the midst of Dell going direct and other OEMs going “how am I going to do direct? We don’t know how to do direct.” We actually worked on a program with Compaq. We were kind of the back office doing what we’ve always done, but to the client it was direct with Compaq. We just facilitated all of it. We were basically pioneering “direct”.
When we opened CBT, with ‘Direct’ being the new delivery vehicle, it was partly focused on the understanding of what the customer wanted and partly what the OEM needed to do to deliver. A lot of VARs at that time were thinking ‘Direct’ was a competitor and a threat. My thing was ‘if you can’t beat them, you need to join them’ so figure out a way to work with them. We were also in the era of IT people working 20-hour days and never seeing their kids; the light at the end of the tunnel was 20 years out with ownership or massive stock being accumulated, and to me that’s just not work-life balance. So, CBT was started on a belief that work-life balance is possible. I believed you could approach the market as a team and make it so that people both had the opportunity of a great career and a great home life.
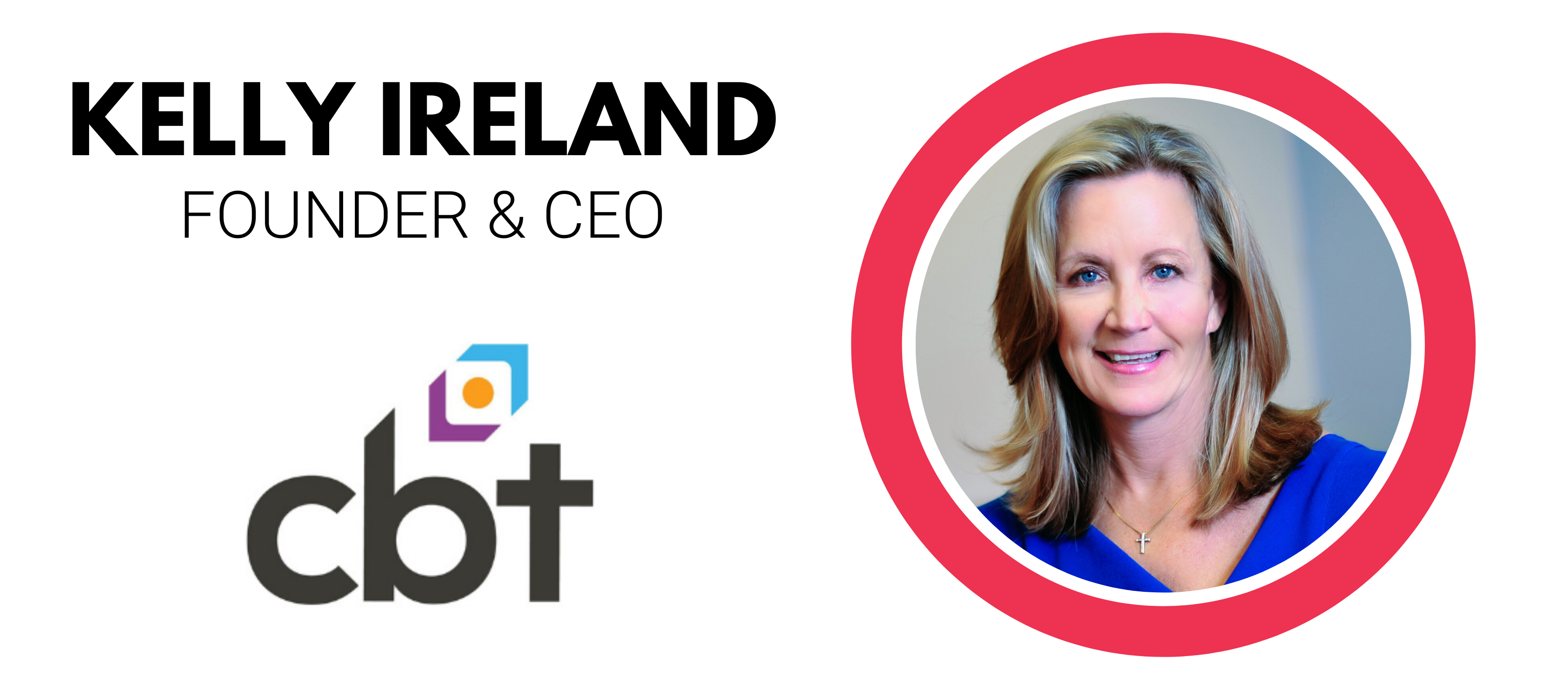
Q: That brings me to another question: What was it like as a woman founder in 2001? I know work-life balance is especially hard for women.
A: I can proudly say I delivered it to my employees. I didn’t get a whole lot of it, but that’s okay. What came out of it is that I have two sons who now have a massive ‘work family’ because they grew up with my employees and I have a lot of employees who’ve been here since 2001. At first it was difficult on my sons, but now they see it as an expansive family they’re still very close to today even in their late twenties and early thirties.
I think I did a good job of attending all their athletic stuff, but you can’t be everything always. I had to travel. I can tell you that being a female in IT, being a founder, it was hard for me to grasp at that point. When we opened, Boeing was our only account and then 9/11 happened three months later. We were instantly in survival mode and I was more worried about that. I think it took me a few years to realize the stigma of being a female owner in IT. There is a stigma and there continues to be; it’s getting better and more balanced, but there’s still a struggle there.
Q: I was going to ask you how it feels to be a female leader today. Can you expand on that a little?
A: It’s not that I don’t respect the ‘All Boys Club’ because that is a relationship, a family, a network and I get it, but it’s unfair to female owners because we can’t be part of that. It’s like we have to work so many times harder to be recognized for what we’re doing, and that’s okay—we’re hard workers anyway, but there’s still an unfairness there. I don’t let it get in my way. When people ask how I’ve handled this in the past, I say that I think I grew up with blinders on. I had really strong females in my family, from my grandmothers to my mom and sisters. I think I just didn’t pay attention to the stigma.
Every once in a while, it rears its ugly head. It’s not so much ‘why am I having to do this’ but why is my team having to work so much harder for less recognition of what they’re doing and achieving? That’s what’s really hard on me. It’s more like I’m the mom and those are my kids and how dare anyone not respect the work they do. I have an amazing team, great workers, and they have such a great mission about work and life, family and community.
If we’re going to take something to a client, we want to test it ourselves.
Q: How has CBT evolved since 2001 and what was the turning point that led you towards wearables?
A: We’ve always gone along with what we see from our clients. So early on, we started pivoting with Boeing to high-performance computing. Boeing was becoming very interested in HPC and I believed we needed to invest. So, I hired internal resources that could support HPC for Boeing and other clients. I’m one of those ‘eat your own dog food’ people: If we’re going to take something to a client, we want to test it ourselves. We do beta testing with some of the OEMs. We want to make sure that there aren’t going to be hiccups when it comes to the actual deployment of the solution. When it came to wearables, we were brought in by an OEM, Hewlett Packard Enterprise, for a big project they had going on.
I was known for being one of the VARs who would invest ahead of time. We did it with another large client, building out a B2B portal specifically customized for them. It brought great business. I looked at the HPE project and thought this looks like the future and yes, we’ll invest money and see what comes out of it. We were very excited about wearables, which has since expanded well beyond just the wearables – we’re building out full IoT and Industrial IoT solutions. Currently in this pandemic, as you can imagine, Connected Worker solutions (including wearables) have helped pivot my company to business we can continue doing through shelter in place. And we can help other companies by enabling their remote workforce, as well.
Q: A lot of companies had this on their roadmap but the pandemic is speeding it up because you have to go remote right now.
A: Yes. you have to do it right now. What we’re excited about is we’ve already been doing this for two and half years; we’ve been doing the testing in production and built out multiple use cases. I’ve personally used this technology myself, both from China and from United Arab Emirates last year, to connect in remote experts from the U.S. They were older engineers and didn’t want to travel to what was a Formula One boat race—high-level engineers that had been working on these state-of-the-art engines requiring an understanding of the combination of engine, electronic data coming off the engine and the propeller combination. These experts were able to help the race team decipher all of this from afar while using my iPhone as the hotspot because there was no Wi-Fi! They were just blown away, saying “I feel like I’m standing there.”
Q: How does CBT define IIoT? A connected worker? What’s your vision for that?
A: I’m going to say our approach because we call it a journey. It’s not just hardware, software and integration. We talk about a wearable, which by itself has inherent capabilities, but it’s like a kid opening up a toy at Christmas. He unwraps it and goes to play with it, but when he’s done playing the toy sits in a corner and maybe is never looked at again. It hasn’t delivered a purpose. Our approach is a journey: start small, figure out something you really need to achieve (a goal, issue, cost reduction, etc.) and we walk you through that process, just as if you were developing a software solution.
As you know, there are lots of wearables and there are lots of ISVs (independent software vendors) that have applications for wearables. It’s our job to look at what’s in the market. We already have a list of I think 30 or 40 ISVs that we’ve vetted to augment our solutions. You know, a lot of them have unique capabilities. Some are pretty consistent, some more broad and others more focused. We find the one we feel is right for the client, build it out through the proof of value and expand from there. The customer gets an almost immediate ROI which can be captured, documented and showcased to their CIO, CFO, COO or CEO, proudly showing a reduction in costs, increased efficiency, process improvement, etc. With Connected Worker, it’s a short-term ROI that gives these companies the ability to really get immersive with the tech after we’ve proven the value.
Q: You mentioned the shiny toy that eventually goes in the corner. What makes up a full IoT solution? It’s not just the wearable; what are key pieces people are usually missing?
A: They’re missing the approach of it being a journey. You need to look at it as a full solution, not bits and pieces. We’ve watched wearable companies falter because their technology is amazing but the approach is incorrect. So, the biggest missing part is the approach. Second is the understanding that it’s not that simple: after two and a half years of going through and putting this into production at Refinery of the Future – we’ve done four solutions and have multiple more coming – there are idiosyncrasies. It’s not like you take the computer, add the software and it goes; there are a lot of things to work through. You have to work through connectivity in many ways, whether it’s data or network, whatever it is. There are a lot of little things that have to be learned; it’s kind of a new frontier.
Q: You mentioned Refinery of the Future. Can you describe that a little more?
A: Refinery of the Future is a Hewlett Packard Enterprise project that started about three years ago. Texmark Chemicals’ CEO had been told about a new thing called a ‘smart’ pump. Long story short, he jumped on and asked where he could see this smart pump in action. The answer was “Well, you can’t, because the customer has this under NDA,” so he said we could use his plant and basically gave his production plant over to HPE & the eco-system team as a lab to build out solutions and deploy to him and his team in production. We’ve built out four different solutions all including major OEMs & ISVs both on the OT and IT sides.
Q: It has allowed us, in production, to test out asset integrity, connected workers, video analytics, condition monitoring and preventative maintenance. A big part of the lessons learned is being able to sit in a production chemical plant and build these out, test them and then put them into production. It’s funny when I presented to Shell, they asked how big Texmark is and I told them seven and a half acres. They said something like “that’s tiny compared to us,” so I said “well, would you give us seven and a half acres of your chemical processing plants to build this out to prove the concept?” The response to that was “Oh no, I get your point.” Texmark offered it up and now I’m getting to show others like Shell and tour them through. We can tour our clients through and show how these are working real time.
Q: I think you’re working on something more for manufacturing now?
A: We are. We’re basically replicating everything we and the partners built out at Texmark in an aerospace manufacturing plant in Southern California. And, in fact, despite the pandemic, we are utilizing the Connected Worker Solution to have one of the personnel at that plant be our eyes. We do virtual meetings with him, directing him to the different parts of the plant we need to see or to specific equipment, whatever it is my team needs to see so that we can continue the project. We’ve already ordered up the infrastructure including the network. We’re working on additional sensors, interfaces, etc. That’s all being done via Connected Worker. So, instead of having to stop the process while we stay home, we’re all able to continue virtually.
Q: How does CBT work with enterprises and partners? I know you mentioned working with HPE but also a company like Boeing. How does the ecosystem work and where do you fit in?
A: CBT fits in in the sense that with the investments we’ve made in personnel, starting with HPC and then moving to OT/IT and industrial IoT including control system engineers and mechanical engineers and design engineers, we’re not just a VAR anymore. The OEMs are working with us directly. They can see that CBT has invested and that our team has spend time living in those environments and experiencing the OT/IT convergence & industrial IoT. We’re now being called upon by distributors, OEMs, ISVs to be what Intel is now calling a Domain Expert Integrator. We don’t want to say we’re an SI, because we’re not a consulting firm. We’re the ones that have the real time tactical and strategic experience in these environments.
It’s a paradigm shift in some ways. If you look back a few years, if you were a small reseller and wanted to get into a larger account, you had to have somebody vouch for you and validate your capability and credibility. Now we have the solution that gets us in for the first conversation with the client and then we’re bringing OEMs and ISVs with us. The discussion is really around the solution first. Then, we help determine the specific Use Case and the necessary software (ISV), hardware (OEM), services, etc. That’s when we determine which one of the OEMs and ISVs need to be a part of the solution.
Q: What’s next for CBT? Any exciting future initiatives or projects in development?
A: We’re going global! We’re addressing inquiries from the Middle East, India and the UK. I think we’ve pioneered to the point where our reputation is out there, we know what we’re talking about and we can bring that. We call it ‘toe dipping’—we have clients looking at industrial IoT that just want to dip their toe in. They’re skeptical, and for good reason. I believe many companies felt burned by the Cloud, so they are approaching IoT with required levels of ROI. We’re seeing that loosen up and have clients reaching out from all over the world. We’ve attended and did a small keynote at the Future Factory conference in Saudi Arabia and have teams we’re working with throughout EMEA and I expect we’ll go into additional countries eventually. I just had a conversation yesterday about Africa, so we’re really excited about that.
Q: How is CBT promoting diversity and inclusion, not only in your company but in the tech industry in general?
A: I’m a massive supporter because of what I’ve had to live through. We support multiple charities and foundations, including STEM organizations. I went to India to visit a place called Shanti Bhavan in 2018. I was introduced to them by Jocelyn DeGance Graham who heads up CloudNOW, a cloud network of women. I went there with my data scientist and the president of a company called GenYES, which is all about developing student tech leaders. Shanti Bhavan is a school that educates young, lowest caste Indians from four years old through college. Shanti Bhavan’s mission is to educate these children who are then able to get a very good job at the end of their college degree and use that financial stability to pull their family out of poverty. It’s an incredible program to support and this summer, one of those students who is going to school in Idaho is going to intern with my marketing team. She’s going to spend a few months – it might be virtual now – with our marketing team to give her some practical experience as Marketing is the field she is interested in pursuing.
We provide scholarships for females from Shanti Bhavan and host a large golf tournament charity event for an organization called Uplift Family Services. When we first started working with them 20 years ago, it was pretty much a facility housing wards of the state, children who had been taken from their parents. Just watching these kids; it breaks your heart. The foundation is all about developing these children into viable adults, teaching their parents (if involved) how to be parents and just giving the kids the opportunity to have a successful life. GenYES is another one, a program not specifically for females but one that really helps support and nurture females and diversity in tech. It starts as young as fourth grade in schools throughout the world, developing student tech leaders within schools to support teachers, staff and other students as technical help.
A lot of school districts share a full-time employee, one or two technical IT persons throughout the district, handling 10 schools. GenYES structures it so kids can be the support and build their own portfolios while helping others. When not assisting others, there’s curriculum they can take for specific IT products, certifications for specific OEM jobs, etc. Though the program is small it’s graduated 12th graders that went straight into networking engineer or software development jobs. We’re now seeing multiple states sign up their school districts. Especially with what has happened to schools with COVID-19, had this been established more widely it would have been simpler and incredibly faster to get teachers set up to do online schooling.