April 20, 2023
A convergence of advancements around data collection, artificial intelligence (AI), computing power, and immersive visualization are enabling next-generation digital twins: Highly detailed, interconnected, persistent, and collaborative digital replicas of products, processes, and systems.
We’re already seeing some advanced, long-term use cases for digital twins from global companies and even individual cities, providing the first indications of what the enterprise or industrial metaverse could look like.
The enterprise metaverse begins with digital twins
An enterprise metaverse can be described as a persistent, immersive simulation of an organization’s entire operations. Enterprise metaverses are made up of many interrelated or linked digital twins, each of which corresponds to (i.e., looks and behaves like) a real asset such as a product, piece of equipment, factory, or supply chain.
As opposed to standalone 3D visualizations, the next-level digital twins emerging today are interactive working virtual copies of their physical counterparts. They can represent anything from a single component to an entire building, the ultimate vision being to replicate and connect every asset, workflow, system, facility, and even person within or related to an enterprise in the virtual world.
Types of digital twins
In my research, I discovered several categories of digital twins, none widely used (to my knowledge) but still helpful:
· Components twins: Replicate individual components or parts
· Asset twins: Replicate individual machines
· System or unit twins: Replicate collections of assets
· Process twins: Simulate a business process
· Digital twins of customers: Could be individuals or personas to, for instance, predict the best customer experience
Experts also propose two levels below digital twins: 1) A digital model just replicates a physical object (no data exchange between the physical object and digital model). 2) A digital shadow involves automated one-way data exchange between the physical object and digital model. 3) A true digital twin involves data flowing in both directions: Data is fed into the digital model, and the digital model produces data used to inform the physical object.
How digital twins are created
Any object can be made into a digital twin using real-world data and advanced 3D modeling. The data might come from multiple sources within and outside the organization, including IoT sensors (ex. in/on the physical asset to create a steady stream of real-time data), enterprise resource planning (ERP) systems (partner/supplier systems, too), cameras, and more.
Once created, digital twins can be used to run simulations, generating insights that ultimately support operational decision making. Digital twins can be viewed in XR, ideally with a mixed or virtual reality headset.
Main applications
Data analysis and decision making: The endless simulation possibilities afforded by digital twins help companies make decisions and predictions about all kinds of things before acting in the real world. A digital twin could theoretically span the entire lifecycle of a product or project, from the design stage to end of life or termination.
Digital twins offer a fast, efficient, and sustainable approach to research and development—important benefits as products and processes become increasingly complex and connected. Iterating with digital twins instead of physical prototyping reduces costs, waste, time to market, and defects. When imbued with historical, real-time, and other relevant data, a 3D model becomes a true digital twin used to operate, monitor, and maintain the physical asset or process. Digital twins create data, too. Combined with AI, they open possibilities for the automation of processes and adjustments to reach peak efficiency.
Virtual experiments with digital twins can generate information not easily obtained in the real world: For instance, you might simulate a production line under varying circumstances to predict behavior, create failure models, determine spare parts needs, scale up, etc.; or you might simulate a product's end-of-life to determine how to ultimately recycle it. Digital twins can also be repurposed for training, remote support, marketing, and more.
Real use case: Mercedes-Benz
Mercedes-Benz has been exploring digital twins for several years now. In January, it was revealed that the luxury automaker is using NVIDIA Omniverse Enterprise to prepare for production of its new EV in its Rastatt, Germany plant. Using a digital twin of the factory, Mercedes can simulate new assembly processes without disrupting existing vehicle production. The ability to design and plan production before it’s live helps streamline the plant’s transition to the next-gen vehicle. Moreover, a digital twin of its supply chain would allow Mercedes to quickly react to disruptions and reconfigure assembly lines as needed.
Besides Mercedes, Anheuser-Busch InBev uses a digital twin of its brewing and supply chain to adjust inputs based on active conditions and automatically compensate for production bottlenecks. Lowe’s has been testing digital twins to optimize store operations. Shahi, an apparel manufacturer, uses digital twins of garments instead of physical samples to speed up the brand approval process. California’s SoFi Stadium uses a digital twin to optimize stadium management and operations, and SpaceX operators used a digital twin of the Dragon capsule to monitor and adjust trajectories, loads, and propulsion systems to maximize reliability and safety during transport.
*IoT Analytics released a helpful visual framework for categorizing and describing digital twin use cases.
Challenges
Data availability is a key challenge of digital twins. In some cases, data is lacking, limited, or unreliable. In other cases, there may be a lot of data in different formats. Next-gen digital twins depend on the ability to generate, integrate, and analyze large volumes of data along with the continuing maturation of emerging enabling technologies like AI/ML, IoT, edge computing, etc.
On that note, infrastructure is another challenge: Digital twins require significant upfront investment in computing resources, data storage, etc. They also require expertise in multiple areas such as data analytics, software engineering, and cybersecurity. Moreover, the most cutting-edge use cases call for linking global economies, data stores, and systems—an unimaginable level of collaboration among governments and corporations.
What’s next?
Capgemini reported that over 80% of organizations have ongoing digital twin programs, while McKinsey found that 70% of C-suite technology executives are already exploring and investing in digital twins. That means your competitors are, too. Digital twins that continually update and communicate with the physical world are possible, promising to usher in an era of unprecedented visibility into business and industrial operations.
Image source: NVIDIA
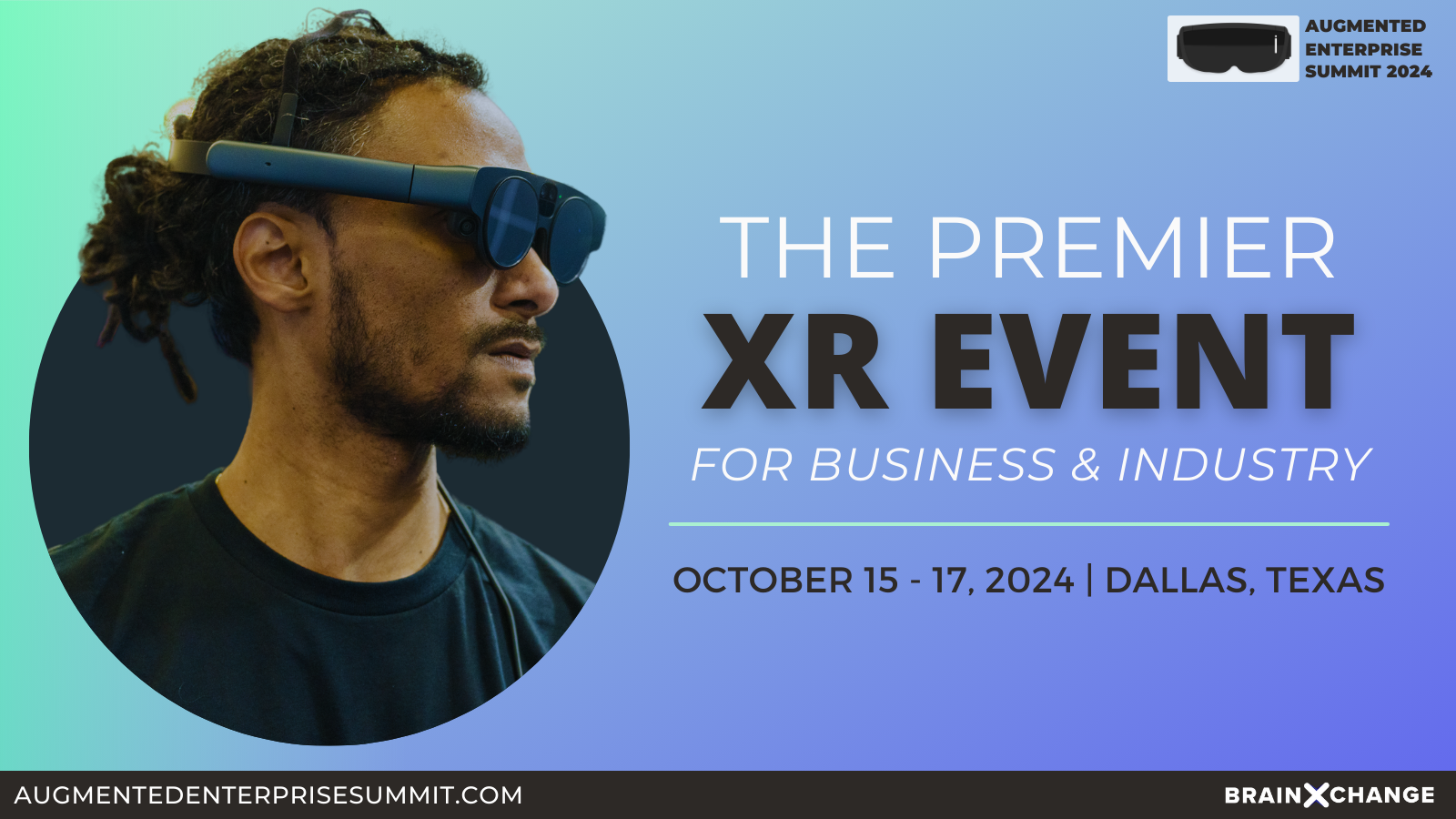